Long Lake Hydroelectric Dam Penstock #1 Rehabilitation
Download PDF version of this case study
With LifeLast’s DuraShield 310 treatment, the Long Lake Hydroelectric Dam’s hundred year old penstock can continue to transport water for clean renewable hydropower generation.
With existing corrosion cells blasted away and long lasting polyurethane wrapping a protective layer around the steel, the Long Lake Hydroelectric Dam’s hundred year old penstock can continue to transport water for clean renewable hydropower generation.
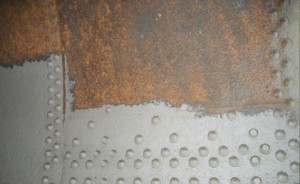
Deteriorating substrate during mechanical blasting
AWWA C222 industry standard compliant for interior and exterior of steel water pipe and fittings. NSF Standard 61 certified formulation of LifeLast DuraShield for NSF/ANSI drinking water and system components. Spokane Lake Reservoir, more commonly known as Long Lake, is 105,000-acre feet of fisheries and recreation paradise for residents of the surrounding communities near the Eastern Washington city of Spokane. Owned by Avista Utilities, this local gem is also a source of green renewable hydroelectric power. Over the years, the power provider has invested in maintaining this asset with work to the generators and adding more efficient turbines to the powerhouse. More recently, the first of four 16-foot diameter penstocks was relined to extend the service life of the original riveted steel pipe. Given the environmental sensitivity of the Columbia River watershed system, Avista Utilities needed a relining solution that minimized the impact on the surrounding ecosystem. DuraShield 310 is recognized by the US Department of Agriculture as a Certified Biobased Product for corrosion prevention. With more than two-thirds of the formulation coming from biobased materials, DuraShield 310 offered an effective Biopreferred® solution. LifeLast worked with Avista to develop a specification that balanced environmental stewardship with economic sensibility.
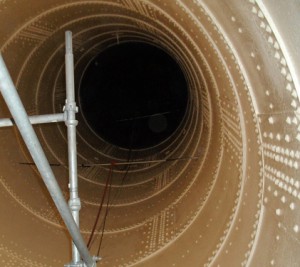
Heated lines and scaffolding were required to access the penstock’s interior surfaces
The 99-year old riveted steel penstock hadn’t been lined since a 1913 application of coal tar epoxy. Heavy pitting and rust scale were present across the pipe surface. The experienced team from Hancock Sandblasting and Paint achieved the SP10 near white finish required in the application specification. Field conditions presented unique spray conditions, particularly the penstock’s 38-degree incline with up to 350 feet of heated lines required to access the workspace. The application team wasn’t in jeopardy of explosive hazards in the confined workspace deep in the penstock’s metallic piping because of DuraShield 310’s VOC-free formulation. The extended pot life of DuraShield 310’s two-part polyurethane system saved the Hancock team time and expense by eliminating the need for a separate hand application to address the irregular surface of this challenging environment. Instead, a crew member was able to ensure adequate coverage by simply following the spray applicator with a brush to wet in the rivets and other irregularities in the penstock surface. This strategy resulted in the specified 40 mils on flat surfaces and 50 to 60 mils elsewhere to ensure rivets were fully encapsulated. Further time and expense was saved in repairs because the polyurethane’s proprietary chemistry minimizes pinholes caused by out-gassing. With the success of this coating application, it may be surprising to learn this was Hancock Sandblasting and Painting’s first experience using a LifeLast product. LifeLast’s Field Service Team partnered with the applicator throughout the project. The relationship began with certifying Hancock to apply LifeLast products. This training included “dialing in” their spray equipment as well as an educational demonstration of the application process. The support didn’t end there, however. LifeLast was onsite at Long Lake with the installation team to ensure field application was successful. The crew applauded the ease of which the product sprayed. Avista Utilities was so pleased with the polyurethane lining application that plans are underway to reline the remaining three penstocks at Long Lake Dam with the same material.

VOC-free formulation didn’t endanger workers in confined spaces
“I was impressed with the application of LifeLast’s DuraShield 310, and the final product is exactly what we were looking for.” -Eric Atkinson, Construction Inspector, Avista Utilities Questions or technical assistance on your specification or project? Contact us; we’re happy to help. Email us at info@LifeLast.com or call (512) 628.2112.