Anacortes Skagit River HDD Crossing
Download PDF version of this case study
Horizontal directional drilling puts pipeline flexibility to the test. The City of Anacortes needed a coating that would not only adhere to the bends of a directional pull, but also stand up to the potentially harsh conditions of a bore to maintain its corrosion protection qualities. They made the right choice: polyurethane lining and coating.
AWWA C222 industry standard compliant for interior and exterior of steel water pipe and fittings. NSF Standard 61 certified formulation of LifeLast DuraShield for NSF/ANSI drinking water and system components.
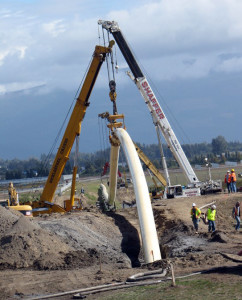
Bending Over Backwards to Get the Job Done
Prospering industry along the Puget Sound and continued population growth in the community of Anacortes, Washington are the kinds of “problems” civic leaders dream about. But the reality of booming business has significant impacts on the demands of local infrastructure. So from 2001 to 2007, Anacortes embarked on a $22.4M construction program to upgrade its existing water transmission main to serve these new demands. The circa 1920’s 24” steel pipeline being replaced had served the community well so they again chose welded steel pipe, capitalizing on advancements in construction and material manufacturing to again ensure a long service life.
One development since the time the original line was constructed was trenchless technology. Specifically, the practice of horizontal directional drilling allowed the City to select a route that went under two local rivers. Segment 5/6 of the project included a 3.2 mile transmission line running from their water treatment plant, adjacent to the Skagit River, to Fidalgo and Whidbey Islands by pulling 1,540 lineal feet of pipe 45 feet below the river bottom. To accomplish this feat, the contractor preassembled long lengths of the flexible polyurethane-coated steel pipes in a staging area and then drug them through a hole created using progressively larger boring heads to tunnel a route for the pipeline to pass through. The largest bore was a 54” head, which created space to uniformly inject bitumen grout around the 36” pipe length as it was pulled through. The pipe forces during the pull reached 300,000 pounds. Sixty mils of interior and exterior LifeLast DuraShield 210 polyurethane stuck with the flexing pipe lengths throughout the installation thanks to its strong adhesion properties. Its high abrasion resistance qualities ensured the pipelines would remain cathodically and mechanically protected from the surrounding soil chemistry.
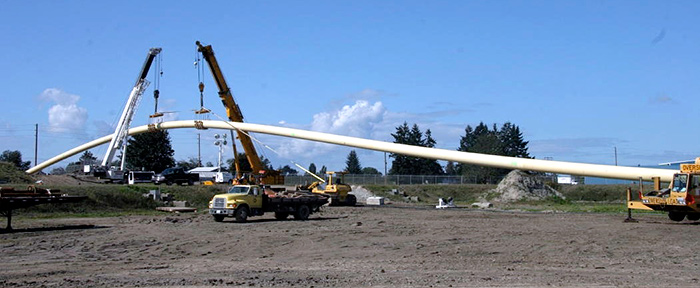
Crews Strung Preassembled Pipe Lengths Through the Air to Feed into the Drill Pit Hole
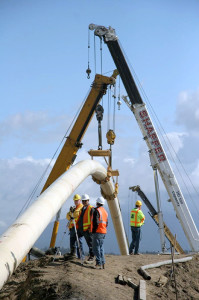
LifeLast Held Firm as the Steel Pipe Flexed on the Elevated Rollers
One noteworthy benefit to selecting polyurethane lined and coated steel pipe for the horizontal directional drill: field joint repair. Joint and Repair System (JARS) Kits provided by LifeLast created continuous cathodic protection barriers to the interior and exterior double lap welded field joints. This simple kit cured quickly, required only basic preparation and allowed the installation contractor to pull the entire pipeline through the hole without having to pause for joint assembly. The result: in less than a single work shift, crews completed the final pull, passing under the river to create a water transmission system that doesn’t mar the scenery or disrupt waterway habitat.
Questions or technical assistance on your specification or project?
Contact us; we’re happy to help. Email us at info@LifeLast.com or call (512) 628-2112.