Brightwater Sewer Conveyance System
Download PDF version of this case study
It takes creative engineering to construct and test a tightly fitted pipeline inside a long, skinny tunnel. DuraShield linings and coatings were tough enough to handle foot traffic and equipment dragged across its surface.
AWWA C222 industry standard compliant for interior and exterior of steel water pipe and fittings.
NSF Standard 61 certified formulation of LifeLast DuraShield for NSF/ANSI drinking water and system components.
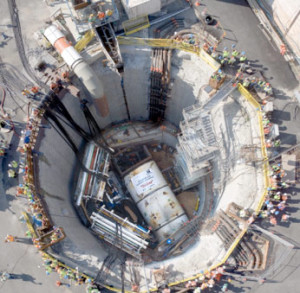
Brightwater tunnel entrance
Washington State’s King County began construction of The Brightwater Conveyance System, a new wastewater treatment facility and pipeline, as a part of a master plan developed to respond to growth in the greater Seattle area. This massive undertaking, estimated at $1.8B, will ultimately provide secondary treatment capacity of 36 million gallons per day. It will flow through more than 13 miles of tunneled influent and effluent conveyance lines, five tunnel portals/shafts, micro-tunneled influent and outfall connections, a large pump station and a 1 mile long marine outfall extending to a depth of 605 feet in Puget Sound.
Jacobs Engineering specified LifeLast’s DuraShield 210 lining for the East Tunnel pipeline, DuraShield 210-61 (NSF Certified) lining with DuraShield 210 coating for the outfall pipeline and DuraShield 210 lining and coating for portions of the wastewater treatment plant piping. The linings and coatings were selected as part of a thoroughly vetted evaluation process of LifeLast’s polyurethane.
The evaluation included analysis of DuraShield 210’s physical properties, independent test data and case histories dating back to the 1980’s. In total, 32,000 lineal feet of 84” and 27” effluent pipe and 32,000 lineal feet of 66” and 48” influent pipe were lined with DuraShield 210 and 1,000 lineal feet of outfall and treatment plant pipe were lined and coated with DuraShield 210 at Northwest Pipe Company’s Portland, Oregon facility. The project is scheduled to be fully operational in 2012.
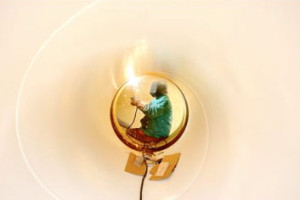
Joint welding conducted in the treatment plant pipe
During the tunnel construction, LifeLast worked closely with the contractors and engineers to ensure the grout port lining was accommodated properly and to act as a technical resource for the team. The pipeline itself acted as the tunnel once the pipe was installed; this is a very high traffic environment due to the access limitations. During last site inspection, an evaluation of the lining was conducted and as expected, the lining was handling the wear flawlessly.
Questions or technical assistance on your specification or project?
Contact us; we’re happy to help. Email us at info@LifeLast.com
or call (512) 628.2112.